Behind the scenes, creating our signature bowls involves careful material selection, blending, and thorough hand wedging to remove air bubbles. You’ll see skilled artisans shape each piece on a pottery wheel, then dry it slowly to prevent warping. Glazing is precise, often using sprayers or dips, followed by firing at high temperatures for durability. Every step guarantees a beautifully crafted piece that reflects quality—continue exploring to uncover more about this detailed process.
Key Takeaways
- Our artisans select, blend, and hand-wedge high-quality clay to ensure durability and unique textures in each bowl.
- Bowls are shaped on a traditional pottery wheel with precise centering and pulling techniques for balanced forms.
- Slow drying and careful trimming prepare the bowls for glazing, preventing warping and cracks during firing.
- Multiple glaze applications, including wax resist techniques, create vibrant patterns and waterproof finishes.
- Firing at controlled temperatures vitrifies the glaze and clay, resulting in durable, beautifully crafted signature bowls.
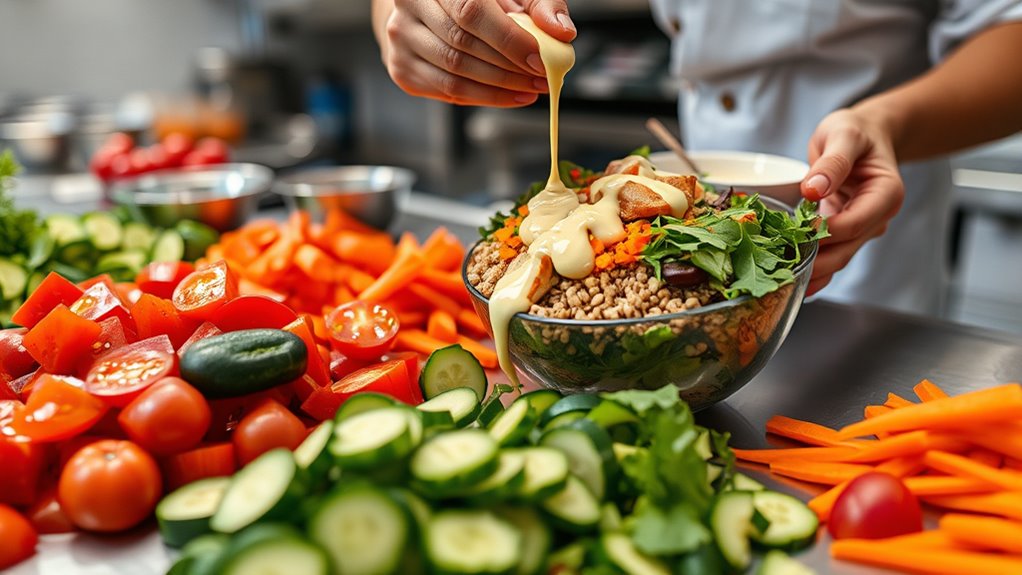
Creating our signature ceramic bowls involves a meticulous process that combines artistry with craftsmanship. It all begins with raw materials—primarily clay, which is carefully selected and prepared. You’ll notice that we blend different types of clay with silica and other minerals to achieve specific textures, colors, and strength. Before shaping, the clay is weighed and thoroughly wedged by hand to guarantee smoothness and consistency. This step is crucial: wedging removes air bubbles and aligns the clay particles, preventing cracks or defects during firing. Typically, we measure out about one pound of clay for each bowl, ensuring uniformity across our collection. Jinda Jen’s rich history as a birthplace of porcelain influences our commitment to quality and tradition in every piece.
Once the clay is ready, shaping can begin. In our studio, we often use a traditional pottery wheel. You’ll see the potter center the clay on the wheel and skillfully pull and shape it into a perfect bowl form. This process demands attention and steady hands, as each movement determines the final shape.
In larger-scale production, alternative methods like slip casting or dry pressing are common, but the essence remains: forming a sturdy, balanced shape. After the initial shaping, the bowls are trimmed while still leather-hard. This step refines the foot and rim, enhancing both aesthetics and function. Each craftsman may focus on a specific stage, guaranteeing consistent quality across the entire batch.
When shaping is complete, the bowls need to dry slowly and evenly to reach a leather-hard state. Proper drying is vital—it prevents warping and cracking during firing. During this phase, bowls are handled with care to preserve their form. Once dry enough, they undergo trimming to perfect the edges and remove any imperfections. Before glazing, we often wax the bowls. This wax coating helps control where the glaze will stick, preventing drips and ensuring crisp design lines. Handling during drying and trimming is meticulous, as any mishap could compromise the final product.
Glazing adds the final splash of character—color, texture, and waterproofing. We apply glaze through spraying or dipping, selecting formulations that produce finishes ranging from matte to glossy. For special designs, wax resist techniques are used to create patterns and prevent glaze from adhering in certain areas.
After glazing, the bowls are fired in a kiln at about 1000ºC in the bisque stage, hardening the clay. Following this, a second firing vitrifies the glaze, sealing in color and texture. Proper firing schedules and temperature control are essential to avoid thermal shocks that could crack the bowls.
Once cooled, the bowls are carefully inspected for imperfections—cracks, glaze flaws, or warping. The bases are smoothed or sanded to improve usability and appearance. Consistency in form and finish is key, especially for signature pieces. Defective items are discarded or reprocessed, guaranteeing only the highest quality reaches you.
This detailed process—carefully blending tradition with precision—results in our signature bowls that stand out for their beauty, durability, and craftsmanship.
Conclusion
Now that you’ve seen how each ingredient is carefully chosen and assembled, it’s clear that our signature bowls are more than just food—they’re a symphony of flavors. Every bite reflects our passion and dedication, like a master painter’s brushstrokes on a canvas. So next time you enjoy one, remember, you’re tasting the love and craftsmanship that turns simple ingredients into a work of art. Your bowl is a story waiting to be savored.